COMMISSIONING MANAGEMENT
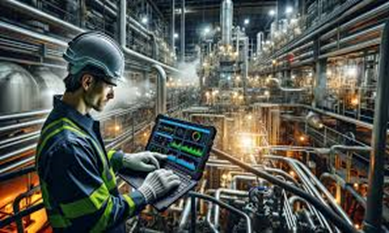
COMMISSIONING MANAGEMENT
The commissioning management phase of industrial plants is a critical stage that ensures all systems and components are installed, tested, and integrated properly before the plant is handed over for operation. By following below steps, the commissioning management phase ensures that industrial plants are thoroughly tested and ready for safe and efficient operation before being handed over to the client. Effective commissioning management is essential for minimizing startup risks, optimizing plant performance, and maximizing asset value.
Steps involved in COMMISSIONING MANAGEMENT
- Pre- Commissioni ng Preparation
- System Walkdowns and Inspections
- Mechanical Completion
- Electrical and Instrumentati on Verification
- Pre-Commiss ioning Testing
- Integrated System Testing
- Functional Testing
- Performance Testing
- Documentation and Reporting
- Operator Training
- Handover to Operations
- Post-Commis sioning Support
Frequently Asked Question
Commissioning Management Services involve planning, coordinating, and overseeing the commissioning phase of industrial plant projects. This includes verifying that all systems and components of the plant are designed, installed, tested, operated, and maintained according to the operational requirements.
These services are crucial for ensuring that the plant operates as intended, meets performance requirements, and complies with safety and regulatory standards. Proper commissioning helps prevent issues during operation, enhances reliability, and extends the lifespan of the plant.
Roles and Responsibilities
Responsibilities include developing commissioning plans, coordinating with project stakeholders, conducting system and component tests, verifying compliance with design specifications, managing commissioning teams, troubleshooting issues, and documenting results.
While Construction Management Services focus on overseeing the construction phase, Commissioning Management Services ensure that the completed construction meets operational and performance standards through rigorous testing and verification processes.
Processes and Procedures
The typical steps include pre-commissioning (preparing systems for initial operation), commissioning (testing and verifying systems), startup (bringing the plant into operation), and post-commissioning (ensuring ongoing performance and addressing any issues).
Tests and verifications are conducted through a series of checks, including functional tests, performance tests, safety tests, and inspections. These are done to ensure that each system and component meets the required specifications and operates correctly.
Tools and Techniques
Common tools include commissioning management software, testing and measurement instruments, checklists, documentation tools, and systems for tracking issues and resolutions.
Safety is ensured by adhering to safety protocols, conducting risk assessments, providing safety training, using personal protective equipment (PPE), and ensuring that all safety systems are tested and operational before the plant goes live.
Best Practices
Best practices include thorough planning and documentation, clear communication with stakeholders, rigorous testing and validation procedures, proactive problem-solving, and continuous monitoring and adjustment during the commissioning process.
These services ensure that the plant operates as intended, meets all performance criteria, and is safe for operation. This reduces the risk of operational issues, enhances efficiency, and ensures a smoother transition from construction to full operation
Industry-Specific Questions
Changes are managed through a change control process that involves assessing the impact of changes, updating commissioning plans and schedules, obtaining necessary approvals, and communicating changes to all relevant stakeholders.
Documentation is crucial for recording test results, compliance with specifications, issues encountered, and resolutions. It provides a comprehensive record of the commissioning process and serves as a reference for future maintenance and troubleshooting.
Compliance is ensured by staying informed about relevant regulations, conducting thorough tests and inspections, maintaining detailed records, and working closely with regulatory authorities to ensure all standards are met
Key challenges include coordinating multiple stakeholders, managing tight schedules, ensuring system integration, addressing unforeseen issues, maintaining safety, and ensuring all systems meet performance criteria
Sustainability is integrated by ensuring that systems operate efficiently, minimizing waste and emissions, using eco-friendly materials and processes, and verifying that sustainability goals are met during the commissioning phase.
Coordination is achieved through detailed planning, regular communication between construction and commissioning teams, phased commissioning schedules, and ensuring that construction milestones align with commissioning requirements.
A commissioning plan outlines the scope, objectives, procedures, and responsibilities for the commissioning process. It typically includes schedules, test procedures, safety protocols, resource requirements, and documentation standards.
What We Provide
Have Additional Questions? Contact Us!
Phone Number
+966 56 391 3902
Mail Address
info@reliabletech.sa